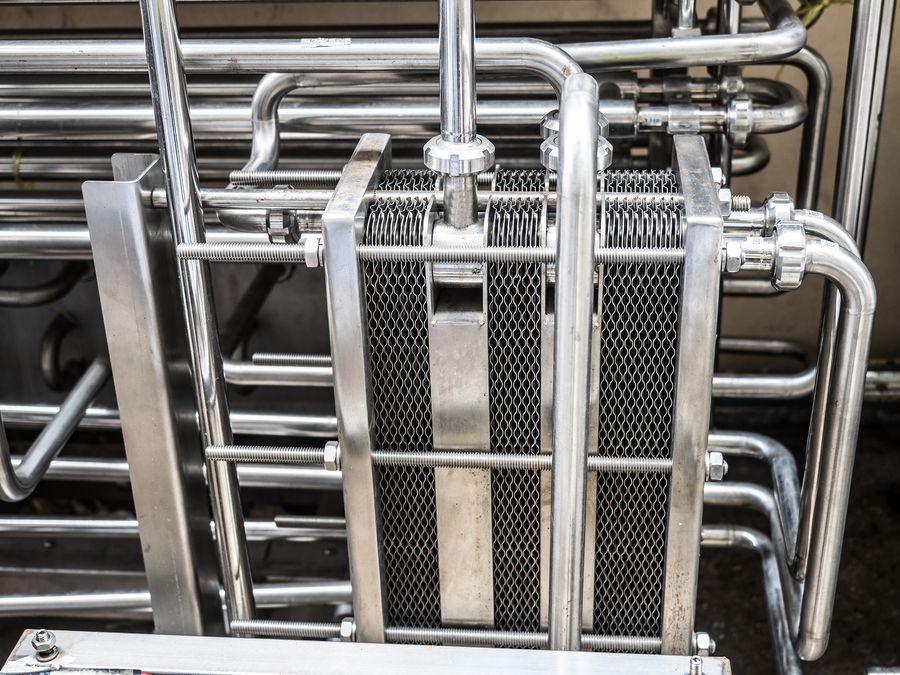
In our last 2 pieces, we firstly looked at plate heat exchangers and their advantages and explained also how they worked. Our third piece in the series now understands just how efficient they in fact are.
Plate heat exchangers are one of the most efficient ways to transfer energy between two fluids at different temperatures whilst keeping both of them separated. Plate heat exchangers are extremely energy efficient, because the energy required usually already exists within the system and can then be easily transferred to another system or process instead of just being allowed to cool down or be pumped out and wasted. The realisation for the need to enhance sustainable energy has never been more prominent. The growing urgency to save and re use energy to reduce environmental impact as well as finding ways to reduce the high cost of energy has placed greater emphasis on utilising the thermal efficiency Plate Heat Exchangers provide. Plate heat exchangers are compact in design and use a series of thin plates such as stainless steel or titanium to transfer heat between two fluids. Plate heat exchangers were first introduced in 1923 for milk pasteurization but are now used in many applications in the HVAC, chemical, dairy, petroleum, refrigeration, pharmaceutical , food processing and health care sectors.
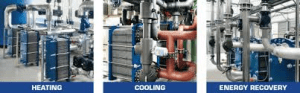
Are Plate Exchangers Efficient?
AEL Plate heat exchanger plates are manufactured in many heights and widths with a selection of various embossed patterns that provide high turbulence at high or low fluid velocities. High turbulence results in very high heat transfer coefficients, with “U” values of 2,000 or more. The U-value is the rate of heat transfer through a plate divided by the difference in temperature across the whole plate structure. The better the heat transfer is the higher the U-value will be. Thermal transmittance takes heat loss due to conduction, convection and radiation into account.
What is “Flow Rate” in a Plate Heat Exchanger
You may have heard the term “volume flow rate” when talking about Plate Heat Exchangers. To simply define volume flow rate it is the volume flow rate of (say water) that is passing through an area such as a pipe that can be measured per unit / time for example litres per second. For example a commercial wash down facility may have hoses with lances that require a total flow of 5 litres of water per second at 70 oC so the volume of water that the Plate Heat Exchanger must deliver at the correct temperature is 5 litres per second. The volume flow rate and temperature required on the secondary flow out of the plate heat exchanger is the prime consideration when designing a plate heat exchanger for a project.
What is “Pressure Drop” in a Plate Heat Exchanger
When a flow is disturbed, a pressure drop (?P) is created, i.e. the flow pressure when the fluid enters the plate heat exchanger is higher than when it is about to exit. Pressure drop always occurs in a plate heat exchanger during the heat transfer process. Excessive pressure drop is not ideal because the flow must then be pushed through the Plate Heat Exchanger using pumps which may require excessive pump power. Large pumps are costly and demand a large amount of electricity which can make the initial cost of installation and ongoing running costs too expensive. The positive side of a manageable pressure drop is that it creates turbulence which is desirable in Plate Heat Exchangers as it improves heat transfer and has a scrubbing effect on the plates removing any deposits. The pressure drop in a Plate Heat Exchanger can be managed by selecting the most suitable plate pattern or a mixture of plate patterns (see below ).
e.g Plates with wider chevrons give a higher pressure drop with more turbulence compared to those with a more narrow angle as does a smaller connection on the flow / return port sizes . The plate pattern and port size are taken into consideration when designing a plate heat exchanger for a project.
How to Size a Plate Heat Exchanger
Please see the information below that is required to design and size a plate heat exchanger.
- The amount of heat available on the Primary circuit to be transferred ( KW heat load)
- The available inlet and outlet temperatures on the primary side
- The maximum allowable pressure drop on the Primary side
- The desired inlet and outlet temperatures on the secondary side
- The maximum allowable pressure drop on the secondary sides
- The amount of KW power required on the secondary circuit to achieve the performance required
- The maximum operating temperature
- The maximum operating pressure
NOTE: The flow rate, specific heat and temperature difference on one side are required to calculate if the heat load is sufficient to do the duty required.